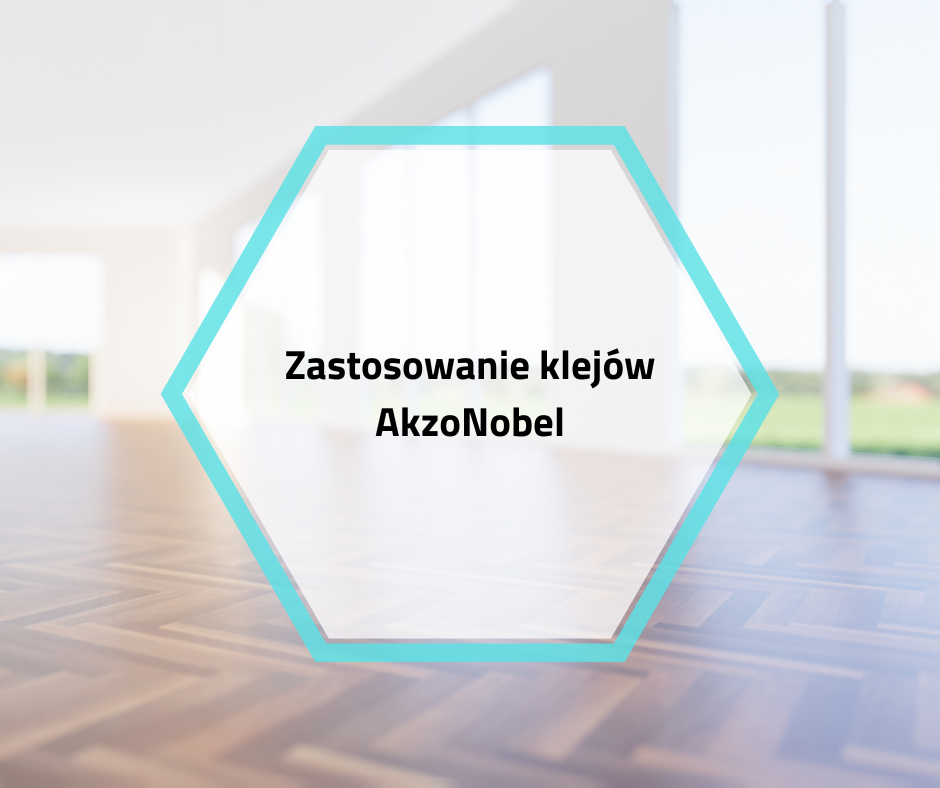
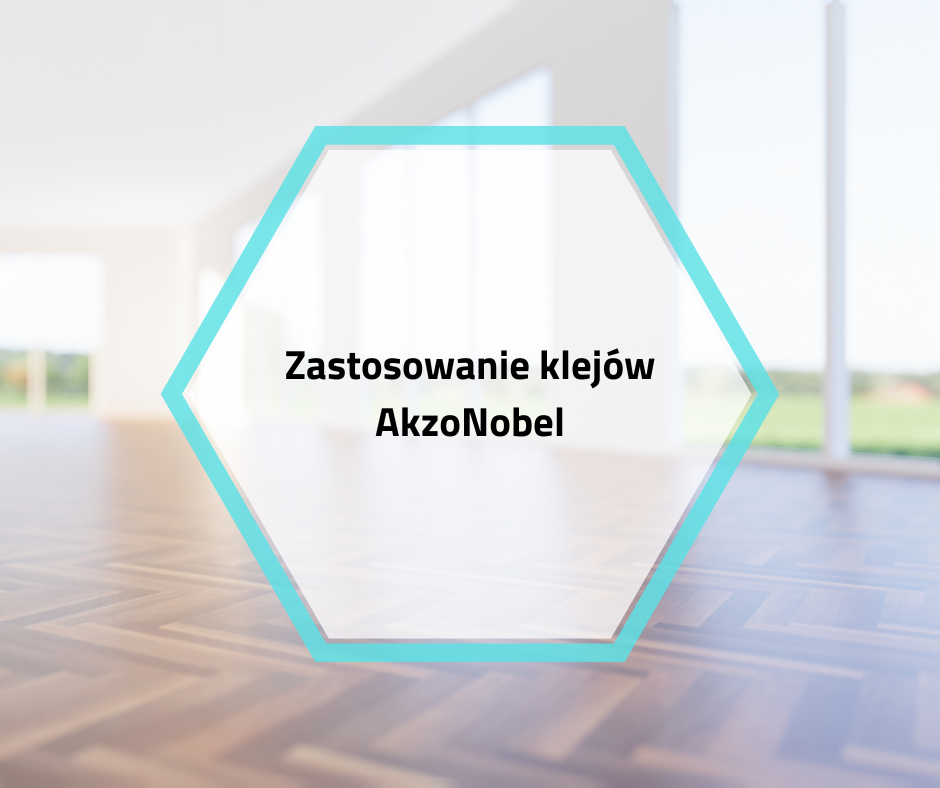
Jesteś ciekaw, w jaki sposób pomagamy usprawnić produkcję naszych klientów przy wykorzystaniu kleju AkzoNobel? W tym case study się tego dowiesz, ponieważ przedstawimy kilka jego zastosowań.
Wykorzystanie kleju do produkcji podłóg warstwowych
Jeden z naszych zaufanych klientów, produkuje deskę podłogową dwuwarstwową. Przez ostatnie kilkanaście lat firma klienta uzyskała znaczącą pozycję na rynku europejskim w zakresie produkcji desek podłogowych. Aktualnie zakład zatrudnia około 200 osób. A bramy zakładu opuszcza codziennie 1500 metrów kwadratowych desek podłogowych. Co więcej, klient stale chce się rozwijać. Jednocześnie ma na uwadze rosnące ceny surowców w związku z czym poszukuje oszczędności. Z tego powodu zaprosił nas, abyśmy przeprowadzili audyt aktualnego procesu produkcji deski podłogowej. A dokładnie klejenia sklejki z obłogami dębowymi. Klient, nauczony wcześniejszymi doświadczeniami, wymagał od nas zapewnienia, aby produkty, które będziemy oferować, nie zmieniły swojego składu chemicznego w trakcie naszej współpracy.
W trakcie wizyty u klienta obserwowaliśmy, w jakich warunkach oraz w jaki sposób przeprowadzany jest proces klejenia. Zauważyliśmy, że elementy przepuszczane są przez nakładarkę walcową. Następnie umieszczane są w prasie pionowej po 78 desek, gdzie pod naciskiem są sklejane. Czas klejenia elementów w prasie wynosi 45 minut.
Zaproponowany klej AkzoNobel
W naszej ocenie klient największe korzyści mógł uzyskać, skracając czas prasowania elementów. Zaproponowaliśmy jeden z klejów AkzoNobel. Po jego zastosowaniu skróciliśmy czas prasowania z 45 do 10 minut, a więc aż o 75%. Dodatkowo poprawiliśmy wytrzymałość powstałej spoiny klejowej, co zostało poświadczone przez Instytut Technologii Drewna. Przy współpracy z nami i zmianie produktu klient zwiększył wydajność produkcji z 1500 m2 na 6000 m2 dziennie. Oznacza to aż czterokrotne zwiększenie wolumenu produkcyjnego.
Opracowanie i dostosowanie technologii klejenia podłogi trójwarstwowej
Wstrzymanie importu sklejki z Białorusi i Rosji wpłynęło na drastyczną podwyżkę cen tego surowca. Wielu producentów podłóg drewnianych stanęło przed koniecznością weryfikacji zasadności produkcji deski dwuwarstwowej oraz niespotykaną dotychczas rekalkulacją kosztów. Wielu z nich stawia sobie pytanie, jak utrzymać produkcję deski podłogowej na obecnym poziomie, jednocześnie nie zwiększając drastycznie cen swoich produktów. Klient, z którym nawiązaliśmy współpracę, doszedł do wniosku, że najlepszym rozwiązaniem będzie zmiana technologii produkcji. Alternatywną opcją dla podłóg drewnianych dwuwarstwowych, gdzie nośnikiem jest sklejka, jest produkcja podłóg trójwarstwowych. Klient, będąc bardzo zadowolony ze zwiększenia wydajności produkcji deski dwuwarstwowej, poprosił nas o wsparcie w klejeniu podłogi trójwarstwowej.
Skład deski trójwarstwowej
W podłodze trójwarstwowej podłoga wykonana jest z nośnika w postaci dwóch warstw listewek z drzew iglastych. Najczęściej stosujemy w spodniej warstwie obłóg przeciwprężny, środek wypełniamy listewką iglastą. Wierzchnia warstwa drewnianej deski to lamele ze szlachetnych gatunków drzew. W związku z tym przy produkcji podłogi drewnianej możliwa jest całkowita rezygnacja ze sklejki i wykonanie desek trójwarstwowych z drewna z lokalnych rynków.
Zalety deski trójwarstwowej
Atutem produkcji trójwarstwowej podłogi jest bardzo duże zainteresowanie tego rodzaju deską podłogową przez klientów, jak i wszechstronność zastosowań. Trójwarstwowa deska w odniesieniu do deski podłogowej dwuwarstwowej cechuje się wyższą jakością użytkową oraz wyższą wytrzymałością. Warto jednak podkreślić, że przejście na produkcję podłogi trójwarstwowej wiąże się ze zmianą technologii. Chcąc zoptymalizować cały proces, niezbędny jest zakup specjalistycznej linii produkcyjnej. Zważywszy na wysoką cenę sklejki pomimo konieczności zmiany linii produkcyjnej, opłacalne jest zastąpienie sklejki listewkami i obłogami drzew. W obecnej sytuacji rezygnacji ze stosowania sklejki jako warstwy bazowej zwrócą się bardzo szybko.
Dobór kleju do deski podłogi drewnianej trójwarstwowej
Klient zainwestował w nową linię do produkcji trójwarstwowych desek. Przeprowadzał na niej testy, wykorzystując dotychczas stosowany klej biały. Niestety występowały duże problemy z wytrzymałością i stabilnością spoiny klejowej. Jak wiadomo z poprzednich naszych casów, nowa linia produkcyjna to nie wszystko. Chcąc uzyskać jak najwyższą efektywność produkcji, niezbędne jest odpowiednie dobranie kleju do linii produkcyjnej.
Zaproponowaliśmy klientowi użycie kleju mocznikowego AkzoNobel 1274 w kombinacjach z różnymi utwardzaczami, zależnie od etapu produkcji. W pierwszej kolejności klejona była spodnia warstwa świerku z sosną. Następnie przy zastosowaniu pras pionowych na zimno klejona była obłoga dębowa. Przy zastosowaniu takiej technologii klejenia deski trójwarstwowej uzyskaliśmy większą stabilność i wytrzymałość spoiny, niż stosując klej PVAC. Dodatkowo dla potwierdzenia słuszności wyboru kleju próbki zostały zbadane w laboratoriach pod względem wytrzymałości. Wyniki były bardzo obiecujące. Miłym zaskoczeniem był sam czas potrzebny na sklejenie podłogi. Klient chciał uzyskać czas łączenia desek nie dłuższy niż 30 minut. Po przeprowadzonych testach i ustawieniu maszyn osiągnęliśmy czas 15 minut. Znaczącym wyzwaniem klejenia mocznikiem podłogi trójwarstwowej okazał się wysoki koszt modernizacja walców klejowych z możliwość ciągłego schładzania mieszaniny. Z racji, że linia produkcyjna nie została ukończona, pomimo optymistycznych wyników zastosowania kleju mocznikowego zmuszeni byliśmy znaleźć inne rozwiązanie dla klienta.Ponownie zaproponowaliśmy klej AkzoNobel, który wcześniej dostosowaliśmy do klejenia podłogi dwuwarstwowej. Okazał się to strzał w dziesiątkę. Klej konkurencji, który dotychczas był wykorzystywany przez klienta, wymagał 2-dniowego okresu leżakowania w celu nabrania finalnych właściwości oraz możliwości dalszej obróbki. Nasz klej utwardza się zdecydowanie szybciej. Już po kilkunastu minutach od wyjęcia z prasy, wypływki były twarde.
Kleje AkzoNobel w dużych fabrykach
Kolejne zastosowanie klejów AkzoNobel dotyczy fabryk. Nasz stały klient posiada jedną z największych fabryk stołów i krzeseł w Polsce. Dziennie bramy zakładu opuszcza około 2,5 tysiąca gotowych krzeseł. Oprócz tego fabryka wytwarza porównywalną ilość różnego rodzaju stołów. Wydaje się, że tak duża fabryka, z wieloletnim doświadczeniem na rynku i rzeszą specjalistów, ma wszystko dopracowane i dopięte na ostatni guzik. Niestety. Tak jak w małych firmach, tak i w dużych fabrykach, niezbędna jest nasza pomoc. W tym przypadku było podobnie.
Podczas wizyt i audytów dotyczących różnych procesów odnotowaliśmy, że istniejące technologie są bardzo dobre. Wszystkie procesy wykonane są z zachowaniem najlepszych praktyk. Natomiast dzięki eksperckiej wiedzy naszych specjalistów, znaleźliśmy kilka miejsc wymagających poprawy i optymalizacji.
Proces klejenia
Obszar, na którym zwróciliśmy szczególną uwagę, to proces klejenia elementów nóg do stołów w prasie pionowej. Zaobserwowaliśmy pewne niedociągnięcia. Etapy pracy fabryki ułożone były w sposób, uniemożliwiający zwiększenia wydajności gniazda produkcyjnego. Jednakże zauważyliśmy u klienta możliwość oszczędności, poprzez zmniejszenie zużycia klejów. W trakcie przeprowadzanych prób oraz testów wytrzymałościowych zredukowaliśmy ilość nakładanego kleju. Pomimo zmniejszenia ilości kleju o 30% zachowaliśmy dotychczasową wytrzymałości spoiny klejowej. Osiągnęliśmy to za sprawą udoskonalenia nakładarki kleju. Poprzez to działanie klej nałożony został równomiernie i powtarzalnie, co w pierwotnej wersji nie zawsze było możliwe. Ponadto w trakcie testów pokazaliśmy klientowi możliwości swojej prasy dotychczas niewykorzystywane. Klient stosował prasowanie dwukrotnie. Po prawidłowym ustawieniu prasy elementy mogły być sklejane już przy pierwszym prasowaniu. Nasza rada pozwoliła zoptymalizować prasowanie, aż o 50%, a elementy były gotowe do dalszej obróbki już na 2 dzień. Oprócz przyspieszenia produkcji znacząco zmniejszono obciążenie pracowników, na co wcześniej się skarżyli. Kierownik produkcji był bardzo zadowolony z rezultatu tej zmiany.
Prasa W-CZ, HF
Dodatkowo znaleźliśmy możliwość optymalizacji przy prasie wysokich częstotliwości (W-CZ, HF). W trakcie przeprowadzonych testów opracowaliśmy ustawienia maszyny, tak, że skróciliśmy czas prasowania z 15 do 8-9 minut. Zmniejszenie czasu obróbki elementu na prasie znacząco zwiększyło możliwości produkcyjne zakładu, gdyż była to jedna z najczęściej wykorzystywanych maszyn u klienta. Ponadto elementy, opuszczając prasę, nie wymagały już leżakowania przed przystąpieniem do dalszych operacji. Co oznacza, że nadawały się od razu do dalszej obróbki. Pominięcie etapu leżakowania sprawiło, że zwolniło się miejsce w hali produkcyjnej. Klient rozważa teraz zakup kolejnych maszyn w ramach zagospodarowania wolnej przestrzeni. Celem zakupu jest zwiększenia wydajności produkcji.
"Im bardziej suche drewno, tym lepiej" - Czy na pewno?
W ostatnim czasie klient zgłosił reklamacje dotyczące rozklejania się połączenia czopowego w konstrukcjach krzeseł. Zdziwiła nas ta sytuacja. Od wielu lat współpracujemy z tym klientem i z powodzeniem dostarczamy kleje do tych połączeń. Nigdy wcześniej nie otrzymaliśmy żadnego zgłoszeń w tej sprawie. Odwiedziliśmy klienta i przeprowadziliśmy audyt, aby znaleźć najlepsze rozwiązanie. Po intensywnych poszukiwaniach źródła problemu odkryliśmy jego przyczynę. Powodem rozklejania się połączeń było drewno, a dokładniej niski poziom jego wilgotności. Często powtarzanym przez wielu stolarzy stwierdzeniem jest to, że drewno musi być suche, a im bardziej suche, tym lepiej. Jest w tym wiele prawdy, lecz drewno nie powinno być zbyt suche – a dokładnie z tym tutaj się spotkaliśmy. Drewno miało zaledwie 4% wilgotności. Suche drewno jest dobrym materiałem do dalszej pracy, tylko trzeba umieć z nim pracować. Należy pamiętać, że suche drewno jest bardzo higroskopijne i chłonie wilgoć z otoczenia oraz środków używanych w trakcie obróbki. W konsekwencji drewno może zacząć się paczyć, rozklejać oraz zmieniać wymiary w najmniej oczekiwanym momencie.
W przypadku naszego klienta bezpośrednią przyczyną rozklejania się drewna był sposób ułożenia cyklu produkcyjnego. Gniazda i czopy wykonywane były w innej części zakładu, niż miejsce, w którym były później klejone. Zrobione były z bardzo dużą precyzją i dokładnością, dzięki czemu idealnie do siebie pasowały. Problem pojawiał się w momencie oczekiwania na sklejenie. Proces ten często rozpoczynał się dopiero po paru dniach od wyfrezowania połączeń. Gniazda i czopy, chłonąc wilgoć, zmieniały swój rozmiar i spasowania. W konsekwencji wcześniej idealnie pasujące połączenie zaczęły wykazywać duże luzy. Klej, który dotychczas był używany, wymagał, aby klejone powierzchnie ściśle do siebie przylegały, ponieważ tylko wtedy można zagwarantować odpowiednią jakość i wytrzymałość spoiny klejowej. Dodatkowo klej miał niską zwilżalność powierzchni i pomimo wchłonięcia wilgoci z otoczenia przez parę dni, drewno nadal było zbyt suche, aby zostało prawidłowo sklejone aktualnie używanym klejem. W zbytnio przesuszonym drewnie pory ulegają zamknięciu i klej nie może właściwie spenetrować klejonej powierzchni. Chcąc wyeliminować powyższe przypadki, zaproponowaliśmy klej AkzoNobel charakteryzujący się wysoką zwilżalnością powierzchni. Klient jest zadowolony z usprawnienia produkcji i nie zgłasza żadnych uwag do nowego kleju. Po rozwiązaniu problemu rozklejania się krzeseł zaproponowaliśmy klientowi zmianę sposobu zarządzania ruchem towarów między gniazdami produkcyjnymi – tak, aby maksymalnie skrócić czas od frezowania czopów do ich sklejania.
Produkty AkzoNobel mają wiele zastosowań, a kilka z nich przedstawione zostały w powyższym tekście. Więcej na temat naszej oferty klejów AkzoNobel oraz ich specyfikacji znajdziesz w naszym katalogu. Zastanawiasz się, w jaki sposób możesz zwiększyć wydajność swojej produkcji. Zależy Ci na wytrzymałości i gwarancji jakości klejów. Nie wahaj się. Napisz do nas, a wspólnie znajdziemy najlepsze rozwiązanie i odpowiedni klej dla Twojej firmy.